更新日: 2022年5月9日
耐熱合金の切削加工における最適な油剤の選定を目的として,工具先端の観察と抵抗力の測定を行った。被削材を超音波で加振することによる効果は薄く,その原因の1つとして被削材と加振テーブルの固定が不十分であることが示唆された。エマルジョン状の切削油剤を複数用意して抵抗力を比較したところ,工具の刃数とねじれ角が変わると油剤の効果が変化したため,工具形状によって最適な油剤は異なることが分かった。また油剤の分散状態や粘度が潤滑性能に影響を及ぼしている可能性が見出された。
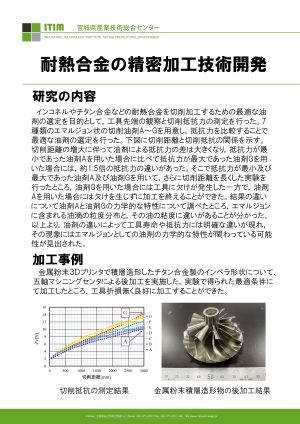
耐熱合金の切削加工における最適な油剤の選定を目的として,工具先端の観察と抵抗力の測定を行った。被削材を超音波で加振することによる効果は薄く,その原因の1つとして被削材と加振テーブルの固定が不十分であることが示唆された。エマルジョン状の切削油剤を複数用意して抵抗力を比較したところ,工具の刃数とねじれ角が変わると油剤の効果が変化したため,工具形状によって最適な油剤は異なることが分かった。また油剤の分散状態や粘度が潤滑性能に影響を及ぼしている可能性が見出された。